مقدمه
در گذشتهای نه چندان دور برای دانشآموزان ژاپنی یک لغتنامه انگلیسی چاپ شده بود که در امتحانات از آن استفاده میکردند. لغتنامه با این عبارت آغاز میشد: «انسان حیوانی است فراموشکار. سعی کن بیشتر از آنچه فراموش میکنی، یاد بگیری!»
واقعیت این است که انسان بسیار فراموشکار است و اشتباه میکند. غالبا ما دیگران را به دلیل اشتباهاتشان سرزنش میکنیم. در محیطهای کاری چنین برخوردی کارکنان را دلسرد و روحیهشان را تضعیف میکند و البته مشکلی را هم حل نمیکند. اینجا است که میتوان از راهحلی ناب استفاده کرد: پوکا- یوکه! تکنیکی برای جلوگیری از بروز اشتباهات ساده انسانی در هنگام انجام کار.
حتما این جملهها به گوشتان خورده است شاید خودتان هم اینگونه فکر میکنید: « مشکل ما چیست؟ چرا ما با وجود انواع روشهایِ کنترلی و استفاده از فناوریهای جدید، باز هم محصول معیوب تولید میکنیم؟ اما ژاپنیها محصول معیوبشان یک در میلیون است؟ به نظرم همهاش شعار است! غیرممکن است در فرایند تولید، هیچ عیبی ایجاد نشود!»
شاید شما هم کمی با مفهوم «عیوب صفر» مشکل داشته باشید و از داستانهای مربوط به کیفیت ژاپنیها و بهرهوریهای آنها خسته شده باشید اما باید به شما اطلاع دهیم که با بازدید از 200 کارخانه ژاپنی، اثبات شده که با ابزارهای ساده پوکا یوکه، واقعا میتوان از وقوع عیب جلوگیری کرد.
پس با هم همراه میشویم تا خودتان ببینید که چگونه این ابزارهای ساده میتوانند به طور مطلق از بروز عیب جلوگیری کنند.
پوکا یوکه (Poka Yoke) چیست؟
در مواجهه با خطا یا عیب، کسب و کارها به دو دسته تقسیم میشوند. دستۀ اول میگویند در فرایندهای ما که فرایندهایِ منحصر به فردی هستند بروز خطا اجتنابناپذیر است و نمیتوان جلوی آن را گرفت. دستۀ دوم میگویند همیشه میتوان جلوی خطا را گرفت به خصوص اگر خطای انسانی باشد حتی در کسب و کار ما!
دستۀ اول از شکایتهای مشتری یا غُر زدنهای فرایند بعدی متوجه میشوند محصول/قطعۀ معیوب تولید شده است. ولی خیلی دیر است چون یا مشتری شاکی شده یا تعداد زیادی محصول/قطعه را باید ضایعات کنند و/یا با دوبارهکاری و صرف هزینۀ دو برابر آن را اصلاح کنند؛ و کارکنانِ آن فرایند یا اپراتورِ آن ماشین را سرزنش و جریمه کنند که چرا محصول معیوب تولید کردهای!!! . دستۀ دوم که معتقدند میتوان خطاها را کم کرد به شرط آنکه ابزارهای مناسب را در اختیار کارکنان قرار داد، به دنبال تکنیکهای پوکا یوکه میروند. جایی که این مقاله شروع میشود.
پس برای صرفهجویی در وقت خودتان هم شده لحظهای درنگ کنید و از خودتان بپرسید شما جزو کدام دسته هستید؟ اگر طرز تفکر شما نسبت به کار خودتان مشابه دستۀ اول است ادامه مقاله فقط اتلاف وقت خواهد بود. اما اگر جزو دستۀ دوم هستید، بدانید که مطالعۀ این مقاله ایدههای جدیدی به شما خواهد داد و برایتان بسیار سودمند خواهد بود.
تفکر و مدیریت ناب (Lean Management) برای ژاپنِ بعد از جنگ دستاوردهای زیادی به همراه داشته است، یکی از با ارزشترینِ آنها پوکا یوکه است.
گرچه مفهوم پوکا یوکه از مدتها پیش مطرح بوده، اما یک مهندس ژاپنی به نام شیجییو شینگو بود که این نظریه را به صورت ابزاری برای رسیدن به عیوب صفر و حذف بازرسیهای کنترل کیفی ترویج داد. منظور از پوکا یوکه، روشهایی است که به کارکنان کمک میکنند در کارهای خود از بروز اشتباهاتی که ناشی از انتخاب نادرست قطعات، از قلم انداختن یک جزء کاری، نصب وارونه قطعه و … است جلوگیری کنند.
پوکا یوکه (Poka-Yoke) اصطلاحی است ژاپنی به معنای “جلوگیری از خطا” که با اجرای ابزارهای ساده و کمهزینه به اپراتورها کمک میکند تا از بروز اشتباه ماشین یا انسان جلوگیری شود. در زبان ژاپنی، “پوکا” به معنای خطای سهوی و ” یوکه” به معنای پیشگیری است. در زبان انگلیسی، پوکا یوکه به خطاناپذیرسازی/ضد خطا (Mistake – Proofing) یا جلوگیری از شکست/خرابی (Fail – Safing) ترجمه شده است.
هدف از پوکا یوکه رسیدن به کیفیت ۱۰۰ درصدی از طریق کشف عیب، در منشاء است. این کار از انتقال عیب توسط اپراتور به مرحله بعد جلوگیری میکند و به تیم اجازه میدهد برای حل مسئله اقدام کنند تا آن عیب دیگر تکرار نشود. دو روش مرسوم در کنترل کیفیت برای شناسایی عیوب عبارت است از (1) نمونهگیری، (2) بازرسی 100 درصدی. در نمونهگیری هیچ وقت نمیتوان با قطعیت گفت که یک دستهی کوچک از نمونهها نشاندهندهی کیفیت کل محصول است. پس اگر نمونهای بدون عیب بود حتما به این معنا نیست که کل محصول بدون عیب است. بازرسی ۱۰۰ درصدی کاری است بسیار پرهزینه و زمانبَر و همیشه این احتمال وجود دارد که باز هم عیبی از قلم بیفتد و در نتیجه محصول معیوب به مشتری یا فرایند بعد برسد. پوکا یوکه با کشفِ محلی که عیب در آن ایجاد شده و همچنین ریشهیابیِ آن، از بروز عیب جلوگیری میکند؛ به جای این که منتظر بمانیم تا عیبی پیدا شود بعد بخواهیم چارهای برایش بیَندیشیم.
اساس پوکا یوکه بر احترام به ذکاوت و هوش کارکنان است. پوکا یوکه با حذف کارهای تکراری و فعالیتهایی که وابسته به حافظه و دقت هستند، وقت و فکر کارکنان را آزاد میکند تا بتوانند وقت خود را به انجام فعالیتهای ارزشآفرین اختصاص دهند.
در یک محیط کار پیچیده، اجباراً بعضی از کارها اشتباه انجام میشوند و احتمالا این اشتباهات به تولید محصول معیوب منجر میشوند. عیوب، اتلاف محسوب میشوند و اگر شناسایی نشوند، مشتری را مایوس و ناراضی میکنند. پوکا یوکه بر این باور است که نباید حتی یک کالای معیوب تولید شود. اما به خاطر داشته باشید که هر پوکایوکهای الزاما خوب نیست، بلکه پوکا یوکههایی خوباند که دارای 3 ویژگی مهم باشند:
(1) ساده و با عمر طولانی بوده و نیاز به تعمیرات و نگهداری کمی داشته باشند؛
(2) کمهزینه باشند؛
(3) برای آن محیط کاری خاص و با توجه به شرایط و نیازهای آن، طراحی شده باشند.
وگرنه بهبودی در کار نخواهد بود و به هدف عیوب صفر نخواهید رسید!
مثالهایی از کاربرد پوکا یوکه
ابتدا چند نمونه رایج از پوکا یوکه در زندگی روزمره را ببینیم و بعد از آن چند نمونه از اجرای Poka-Yoke در صنعت خودرو، به ویژه در تویوتا که خاستگاه آن است را بررسی میکنیم.
نمونههای رایج از پوکا یوکه در زندگی روزمره:
• شروع بکار ماشینهای لباسشویی فقط در صورت بسته شدن درِ آن
• صدای آلارم یخچال هنگام زیاد باز ماندن درِ یخچال
• به صدا در آمدن سوت کتری هنگام به جوش آمدن
• تفاوت پریزهای برق و تلفن
• توقف ماشین چمنزنی در صورت رها شدن میلهی آهنیِ زیر آن از دستِ کاربر
• چراغ راهنمایی رانندگی
نمونههای رایج از پوکا یوکه در محیط کار
• توقف خودکار ارهی رومیزی برای جلوگیری از آسیب
• وجود غلطیاب در نرمافزارهای واژهپرداز مثل Word برای جلوگیری از اشتباهات املایی و گرامری
• پیامِ نوشته نشدن موضوع (subject) هنگام ارسال ایمیل
• استفاده از برچسب هشداردهنده برای داروهای با هشدار بالا در بیمارستان برای جلوگیری از اشتباهات دارویی
• استفاده از چکلیست برای نگهداری دورهای یا روزانۀ تجهیزات
• استفاده از بارکد خوان در سوپرمارکتها و خردهفروشیها برای جلوگیری از اشتباه در قیمت کالا
• استفاده از دستکشهای آبی در صنایع غذایی برای تشخیص راحت از مواد غذایی
• تجهیزاتی که با هر دو دست کنترل میشوند تا فاصلهی استاندارد اپراتور و ماشین حفظ شود
نمونههای پوکا یوکه در تویوتا
• استفاده از سیمکشی با کد رنگی (color code): تویوتا در فرایند مونتاژ از سیمکشی با رنگهای مختلف استفاده میکند. در این تکنیک به هر سیم، یک رنگ خاص اختصاص مییابد که شناسایی و اتصال صحیح سیمها را برای اپراتورهای خط مونتاژ آسانتر میکند. این تکنیک ساده به جلوگیری از اشتباهات سیمکشی و اطمینان از اتصالات الکتریکی مناسب کمک میکند.
• سنسورهای Poka-Yoke در مونتاژ: در تویوتا سنسورهایی در خط مونتاژ نصب شدهاند که در صورت نصب اشتباه یا از قلم افتادن یک قطعه آلارم زده و خط مونتاژ اتوماتیک متوقف میشود.
• ایمنسازی در فرایند رنگکاری: استفاده از سنسورها برای کنترلِ ضخامت و یکنواختی پوشش رنگ در سالنهای رنگ که در صورت بروز عیب، آلارم زده شده و فرایند رنگکاری متوقف میشود.
در واقع، تویوتا با استفاده از این تکنیکها، احتمال خطا را به طور قابل توجهی کاهش و فرایند تولید را بهبود داده است. این مثالها نشاندهندۀ تعهد تویوتا به ارائه وسایل نقلیه قابل اعتماد با حداقل عیب و حداکثر ایمنی است تا هرچه بیشتر مشتریهای خود را راضی و وفادار نگهدارد.
ابزارها و روشهای پوکا یوکه
ابزارهای پوکا یوکه زیاد هستند و استفاده از آنها بستگی زیادی به خلاقیت کارکنان و شرایط محیط کار دارد، به طور کلی ابزارهای پوکا یوکه را میتوان به دو دسته تقسیم کرد:
- ابزارهای متوقفکننده (Shutdown devices) که معمولا در روشهای جیدوکا مورد استفاده قرار میگیرند. یکی از سادهترین و موثرترین متوقفکنندهها انواع سنسورها و جیگهای ساده در فرایندهای تولیدی و خدماتی هستند که به طور اتوماتیک ماشین یا فرایند را متوقف میکنند.
- ابزارهای هشداردهنده (Warning devices) که در روشهای بازرسی در منشأ و بازرسی صددرصدی مورد استفاده قرار میگیرند. یکی از ارزانترین و سادهترین هشداردهندهها، آلارمها یا چراغهای آندن هستند که با تشخیص شرایط غیرعادی هشدار میدهند.
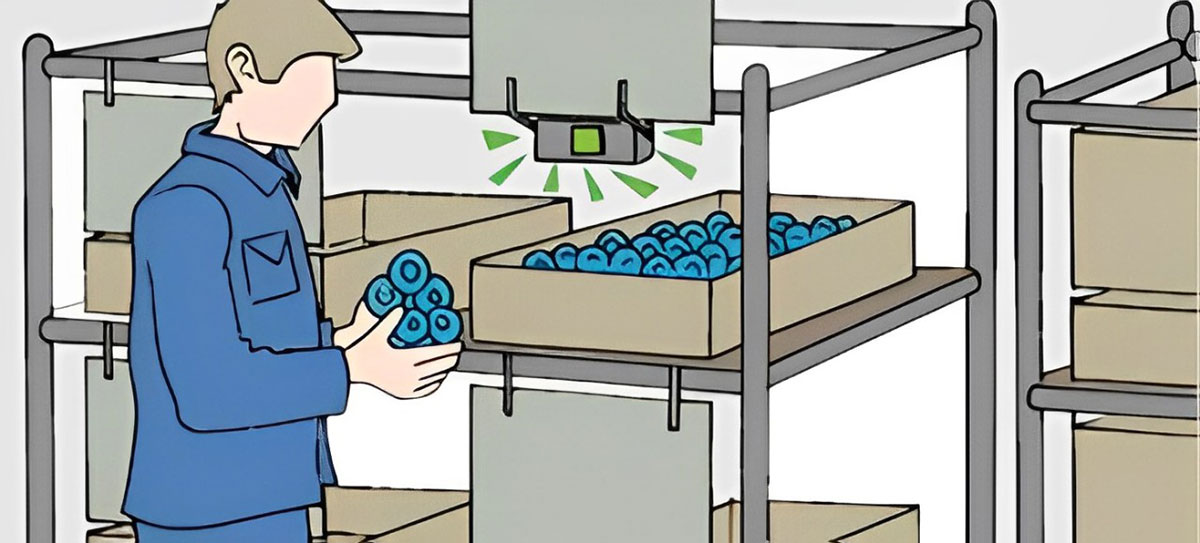
همانطور که گفته شد هر یک از این ابزارها معمولا در تکنیکهای خاصی مورد استفاده قرار میگیرند و یکی از نکاتی که کاربرد ابزارهای پوکا یوکه را برای یک سازمان اثربخش میکند این است که از ابزار درست برای تکنیک درست استفاده شود. تکنیکهای پوکا یوکه در سه دسته طبقهبندی میشوند. در ادامه به بررسی روشهای خطاناپذیرسازی میپردازیم.
1.بازرسی در منشاء به کمک ابزارهای پوکا یوکه (Source Inspection): یعنی شناسایی خطاها در منشأ پیش از آنکه این خطا در مراحل بعدی منجر به بروز عیب شود. مثلا استفاده از یک پرس با سنسور نوری که وقتی محصول فاقد شکل مناسب است عیب را تشخیص داده و بلافاصله آلارم دستگاه به صدا در آید. مثال دیگر استفاده از پینهای کمکی یا جیگهای راهنما است تا حتما قطعه به درستی قرار بگیرد و تنظیم باشد تا قطعه معیوب تولید نشود. اهمیت و اثرگذاری استفاده از این روش در جلوگیری از بروز خطا 60 % است.
۲. بازرسی صد درصدی با استفاده از ابزارهای پوکا یوکه: در این نوع از بازرسی صد درصدی، بازرسی به جای اینکه توسط نیروی انسانی انجام شود که همیشه با احتمال خطا همراه است، به کمک ابزارهای ساده و ارزان انجام میشود. در این نوع از بازرسی هم تک تک محصولات یا قطعات بازرسی میشوند تا مطابق با استانداردهای کیفی تعیین شده باشند مثلا استفاده از کلیدهای حدی، سیستمهای بازرسی خودکار و جیگها. هدف از بازرسی صد درصدی شناسایی و رفع عیب قبل از رسیدن به دست مشتری است و اطمینان از این که تنها محصول/قطعهای به فرایند بعدی/مشتری میرسدکه مطابق با مشخصات مورد نظر باشد. . اهمیت و تاثیر استفاده از این روش در جلوگیری از بروز خطا 30 % است.
۳. توقف یا جیدوکا: (Jidoka): در این روش با استفاده از تجهیزاتی مثل مدار توقف داخلی، محصول معیوب تشخیص داده شده و ماشین به طور اتوماتیک متوقف میشود. در این روش هم به جای اینکه یک نیروی انسانی تمام وقت بالای سر ماشین بایستد تا عیوب را شناسایی کند، از ابزارهای ساده و کمهزینه استفاده میشود تا ماشین متوقف شود. در تویوتا به این روش جیدوکا هم گفته میشود. جیدوکا از تولید محصول/قطعۀ معیوب جلوگیری و به حفظ کیفیت در کل فرایند یا محصول کمک میکند. به اعتقاد شیجییو شینگو اهمیت و اثرگذاری استفاده از این روش در جلوگیری از بروز خطا 10 % است.
با اینکه روش اول، یعنی جلوگیری از بروز عیب در منشأ از دو تکنیک دیگر بسیار موثرتر است، اما تکنیکهای بازرسی صددرصدی و توقف فوری عملیات هم در به حداقل رسیدن عیب و رسیدن محصول/قطعۀ سالم به فرایند بعدی/مشتری بسیار موثرند. تاکید میشود که در پوکا یوکه برای شناسایی عیب و جلوگیری از بروز آن، در هر تکنیک از ابزارهای مخصوص همان تکنیک استفاده شود.
سطوح پوکا یوکه
پوکا یوکه در دو سطح طبقهبندی میشود:
- تشخیص: شناسایی خطاها و عیوبی که اتفاق افتاده است.
- پیشگیری: جلوگیری از خطاهایی که ممکن است پیش بیاید.
قبل از ادامه بحث لازم است دو واژۀ «خطا» و «عیب» را یکبار دیگر مرور کنیم. خطا (mistake) کارهای اشتباهی است که توسط نیروی انسانی یا ماشین انجام میشود که به بروز عیب منجر میشوند. اما عیب (defect) دقیقا اشاره به شرایطی دارد که خودِ محصول یا خدمت با آنچه باید به مشتری نهایی یا فرایند بعدی تحویل داده شود مغایرت دارد. این مغایرت میتواند در مشخصات ظاهری باشد یا در مشخصات کیفی. به همین دلیل در پوکا یوکه عبارتهایی مانند خطاناپذیرسازی (mistake proofing) و جلوگیری از بروز عیب (preventing defects) تِرمهای مصطلح و پر کابردی هستند.
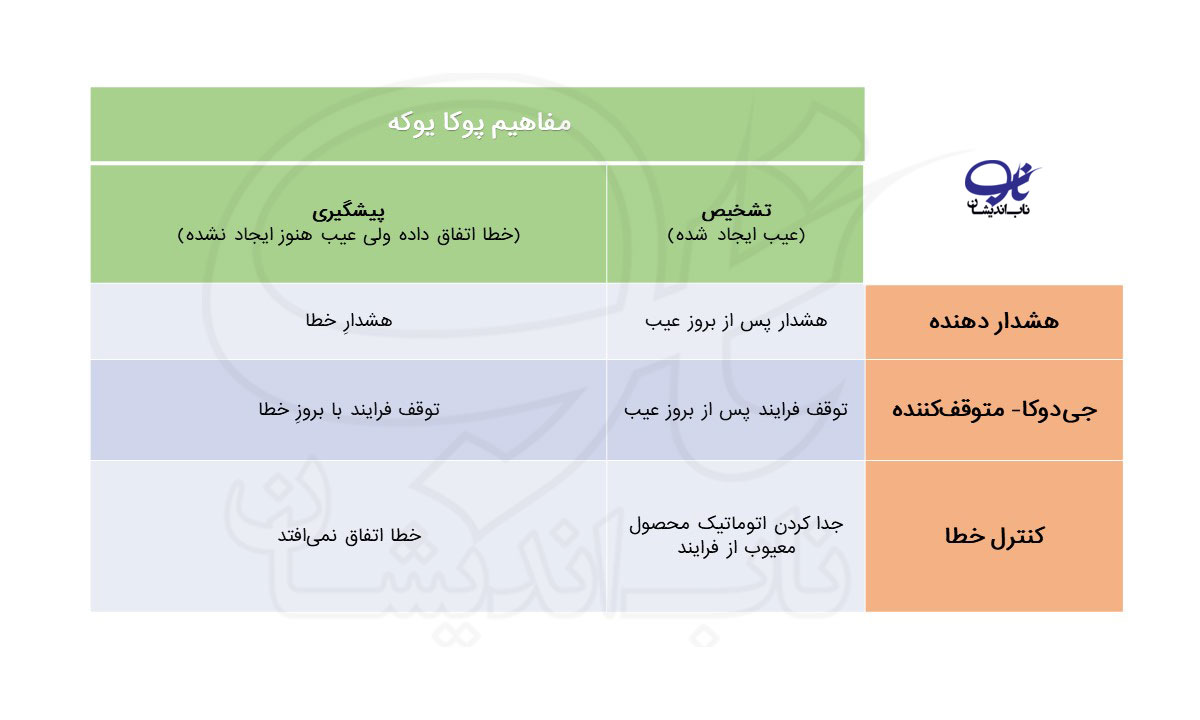
بسته به این که چه سطحی از پوکا یوکه ضروری است که در سازمان پیادهسازی شود، میتوان از همان ابزارهایی استفاده کرد که در قسمت قبل همین مقاله توضیح داده شد. در اینجا دوباره ابزارها را مررو میکنیم و برای استفاده هر کدام در یک سطح معین مثال میزنیم.
هشداردهندهها: این ابزارها فقط میتوانند خطا و عیب یا علتِ آن را تشخیص دهند. سپس به اپراتور در مورد خرابی یا علت خرابی هشدار دهند. اپراتور بعد از دیدن یا شنیدن آلارم در مورد نحوه واکنش به آن تصمیم میگیرد. این سطح پایینترین سطح کنترل است زیرا اپراتور میتواند اخطار را نادیده بگیرد و عیب به فرایند بعدی منتقل شود.
مزیت هشداردهندهها این است که با ابزارهای ساده و ارزان، خطای انسانی یا خرابی را تشخیص میدهند. اما مشکل هشداردهندهها در این است که فقط هشدار میدهند و این اپراتور است که تصمیم میگیرد، خطا نکند یا به همان شیوۀ قبل کار کند. هشدار دهندهها ابتداییترین سطح کنترل هستند چون اپراتور به دلیل شرایط مختلف مثل فشار کاری میتواند آلارم را نادیده بگیرد یا در اثر فراموشی، محصول معیوب به فرایند بعدی منتقل شود.
جیدوکا یا Stop: این ابزارها خطا، عیب و/یا علت آن را تشخیص میدهند و با تشخیص عیب همان لحظه ماشین را متوقف و با تشخیص خطای انسانی، ماشین را قفل میکنند. متوقفکنندهها، سطح بالاتر و ایمنتری از کنترل هستند چون با توقف عملیات یا قفل شدن ماشین، اپراتور مجبور است مشکل را برطرف کند در غیر این صورت نمیتواند به کارش ادامه دهد.
کنترل خطا Error/Defect Control: این ابزارها، بالاترین سطح کنترلاند. ابزارهای هایتک که عیب و علت آن را تشخیص میدهند، سپس قطعه معیوب را اتوماتیک از فرایند خارج میکنند بدون آنکه وقفهای در کار فرایند پیش بیاید. یا با تشخیص خطا آن را اتوماتیک اصلاح میکنند. پیادهسازی این ابزارها بسیار گران است و به دانش مهندسی و سیستم نگهداری و تعمیرات بالایی نیاز دارد. برای مثال در تصویر زیر، بطریای را که دَر ندارد (محصول معیوب) تشخیص داده شده و از فرایند خارج میشود بدون آنکه کانوایر متوقف گردد.
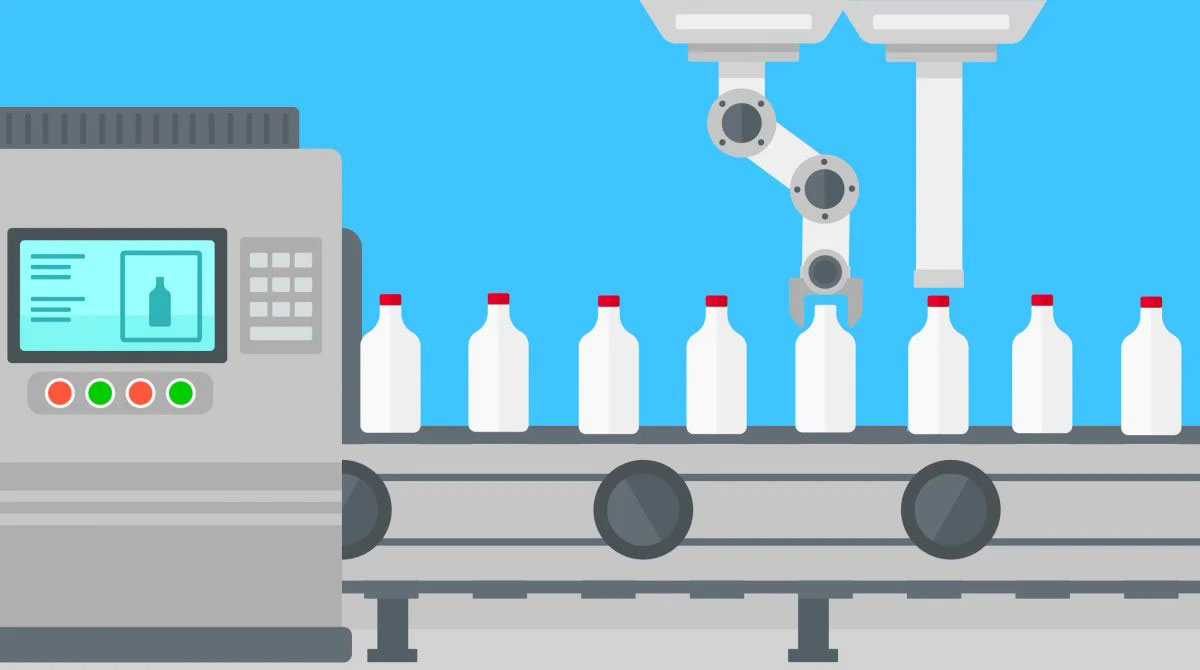
یک مثال برای سطح تشخیص:
نکتهای که باید توجه داشت این است که در سطح تشخیص، خطای اپراتور منجر به محصول معیوب شده است و تمرکز بر این است که با جداسازی محصول معیوب از محصول سالم؛ عیب به فرایند بعدی منتقل نشود.
مثلا در فرایند جوشکاری، اپراتور باید روی قطعه 6 نقطه جوش بزند. اجزاء کاری عملیات به این شرح است: (1) قطعه را روی ماشین بگذار؛ (2) به ترتیب در نقاط معین نقطهجوش بزن؛ (3) قطعه را بردار و در گاری مخصوص بچین.
در طیِ این فرایند چه مشکلِ کیفی ممکن است پیش بیاید؟ ممکن است نقطه جوش کمتر زده شود یا در محل درست زده نشود. حالا میخواهیم به کمک ابزارهای پوکایوکه در این سطح با بازرسی در منشأ جلوی رفتن معیوب به فرایند مونتاژ را بگیریم.
حالت اول – استفاده از ابزارهای هشداردهنده: در این حالت که ابتداییترین حالتِ تشخیص عیب است، شمارنده روی ماشین نصب میشود و همچنین یک لامپ یا آلارم به ماشین اضافه میشود. پس از انجام عملیات و اتمام کار اپراتور، اگر لامپ روشن شود یا صدای زنگ آلارم بلند شود یعنی محصول معیوب تولید شده است. بنابراین اپراتور باید عملیات را متوقف کند، به صورت دستی قطعه را چک کند (1) اگر عیب قابل اصلاح است همانجا اصلاح کند مثلا کنتور تعداد نقطه جوش 5 را نشان میدهد، پس اپراتور باید همان موقع نقطه جوش جا افتاده را بزند؛ (2) اگر محل نقطه جوش نادرست است، قطعه معیوب را جدا کرده و در سبدِ قرمز بگذارد تا دوبارهکاری یا در صورت لزوم ضایعات شود. در این حالت اپراتور میتواند هشدار را نادیده بگیرد و محصول معیوب به فرایند بعدی منتقل شود. و وقتی فرایند مونتاژ میخواهد از این قطعه استفاده کند متوجه میشود یک گاری قطعه دارد که 5 نقطه جوش خورده و دوباره باید به فرایند قبل مرجوع شود.
حالت دوم- استفاده از ابزارهای جیدوکا یا متوقفکننده: در این حالت، یک سنسور نوری، نقطه جوش اشتباه (محصول معیوب) را تشخیص داده و بلافاصله ماشین را متوقف میکند. با این حال، باز هم این اپراتور است که باید قطعۀ معیوب را بردارد و در سبد ضایعات بگذارد و ماشین را مجدد راهاندازی کند. یک مثال دیگر زمانی است که قطعۀ معیوب به فرایند مونتاژ رسیده و اپراتور مونتاژ هنگام مونتاژ نمیتواند قطعه را جا بزند. درنتیجه عملیات مونتاژ متوقف میشود و اپراتور باید قطعه را در سبد قرمز بگذارد.
مشکل این حالت این است که توقف ماشین یا خط مونتاژ، باعث طولانی شدن زمان چرخه تولید و کاهش آمار تولید میشود. مشکل دیگر این است که باز هم جداسازی برعهده خودِ اپراتور است و ممکن است اپراتور فراموش کند قطعۀ معیوب را در سبد قرمز بگذارد و با قطعه سالم مخلوط شود. این مشکل زمانی گران تمام میشود که یک دسته از قطعه/محصول برای مشتری ارسال شود و به دلیل وجود حتی یک محصول معیوب، تمام سفارش مرجوع و شرکت جریمه شود.
حالت سوم- استفاده از ابزارهای کنترل عیب: این حالت بالاترین سطح پوکا یوکه برای تشخیص عیب است. در مثال بالا، پس از تشخیص قطعۀ معیوب، ماشین اتوماتیک متوقف میشود و بدون دخالتِ اپراتور، قطعۀ معیوب در سبد قرمز میافتد که کنار ماشین تعبیه شده است بدون آنکه وقفهای در عملیات صورت بگیرد و زمان تولید از دست برود. یا در مثال تصویر خط تولید شیر که تصویرش در بالا آمده است، سوئیچهای مجاورتی تشخیص میدهند که بطری درپوش ندارد. این سوئیچ به یک کلید تقسیمکننده وصل است. و با تشخیصِ بطری معیوب تقسیمکننده بسته شده و به وسیلۀ یک ربات، مسیر حرکت بطریِ معیوب به سمت فرایند قبلی یعنی مونتاژ درپوش تغییر میکند.
یک مثال برای سطح پیشگیری
در سطح پیشگیری، تمرکز بر این است که جلوی خطای اپراتور گرفته شده و عیب تولید نشود.
مثلا در فرایند دریلکاری، اپراتور باید قطعه را در موقعیت صحیح قرار دهد تا سوراخ دقیقا در محل درست زده شود. اجزاء کاری این عملیات به شرح زیر است: (1) قطعه را روی ماشین بگذار؛ (2) دکمه استارت را فشار بده تا قطعه دریل شود.
در طیِ این فرایند چه مشکلِ کیفی ممکن است پیش بیاید؟ گاهی از روی بیدقتی، فقدان آموزش کافی و صحیح، نبود کار استاندارد روشن یا عجلهکاری ممکن است قطعه روی ماشین به درستی تنظیم نشود و سوراخ در محل درست زده نشود یا قطعه وارونه یعنی در جهت نادرست یا حتی به پشت روی ماشین قرار گرفته و دریل شود.
حالت اول- استفاده از ابزارهای هشداردهندۀ خطا: همانطور که گفته شد این ابزارها ابتداییترین حالتِ پیشگیری هستند چون همیشه احتمال دارد خطا منجر به محصول معیوب یا آسیب به اپراتور شود. در مثال بالا، برای پیشگیری از خطا، تیمِ بهبود پیشنهاد میدهد یک فیکسچر راهنما برای هدایت قطعه در محل درست به ماشین اضافه شود و یک سوییچ حدی هم روی ماشین نصب شود تا در صورت قرارگیری نادرست قطعه یک لامپ روشن شود. پس از پیادهسازی این بهبود، اپراتور قطعه را روی ماشین میگذارد و دکمۀ استارت را میزند. اگر قطعه در محل درست قرار گرفته باشد دریل کاری انجام میشود و اگر قطعه در محل درست جاگیری نشده باشد لامپ روشن میشود و خطا را به اپراتور اطلاع میدهد. از این لحظه به بعد همه چیز بستگی به انتخاب اپراتور دارد که میخواهد جلوی خطا را بگیرد یعنی عملیات را متوقف و قطعه را تنظیم کند یا به هر دلیلی تصمیم بگیرد که کارش را ادامه دهد.
حالت دوم- استفاده از ابزارهای جیدوکا یا متوقفکننده: در مثال بالا، به جای نصب لامپ برای دادن هشدار و اطلاع به اپراتور؛ اگر قطعه در موقعیت درست قرار نگیرد سوییچ حدی به طور اتوماتیک ماشین را متوقف کرده و دریلکاری انجام نمیشود. مزیت این حالت نسب به حالت اول این است که اپراتور نمیتواند کارش را ادامه دهد مگر آنکه قطعه را به درستی تنظیم کند و بدین ترتیب خطای اپراتور به تولید محصول معیوب منجر نمیشود.
حالت سوم- استفاده از ابزارهای کنترل خطا: برای مثال بالا که یک قطعۀ سه بعدی است (عرض،طول و ارتفاع دارد)، اپراتور حذف شود و یک ربات صنعتی همه مراحل را انجام دهد. عیب این ابزارها در این است که نگهداری و تعمیرات آن یک مسئله جدی برای واحد نِت خواهد بود.
تصویر زیر یک مثال دیگر از سطح پیشگیری در پوکا یوکه است.
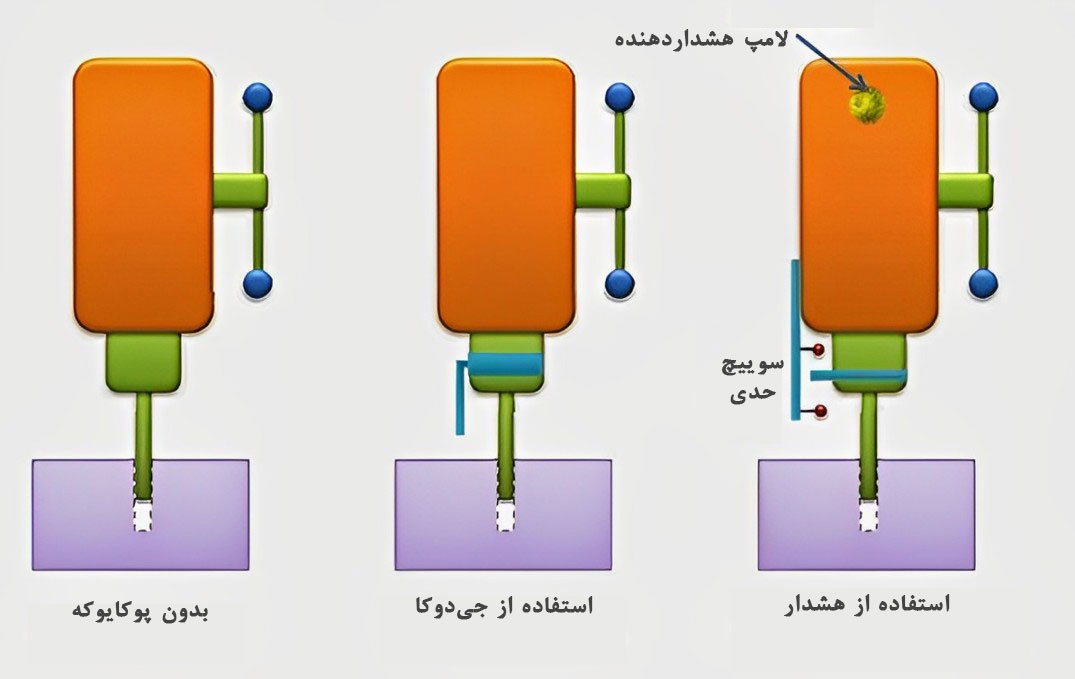
چه موقع از کدام ابزار پوکا یوکه باید استفاده کرد؟
شاید بپرسید کدام ابزار را باید برای فرایندهایِ خودمان انتخاب کنیم؟ از کجا بفهمیم ابزار مناسب ما کدام است؟
برای پاسخ به این سوال، باید از الزامات فرایند شروع کنید. مثلا از PFMEA برای یافتن سطح ابزارهای کنترلیِ مناسب در پوکا یوکه استفاده کنید. تکنیک آنالیز حالات شکست/خرابی و اثرات آن (Process failure mode and effects analysis) یکی از زیرشاخههای تکنیک FMEA است.
در این تکنیک درجهبندی شدت خرابی، رتبهبندی تکرار بروز عیب، و ارزیابی و رتبهبندی ابزارهای کنترلی (از آسان به پیچیده) برای هر ماشین و عیوب آن مورد مطالعه و بررسی قرار میگیرد. سپس با محاسبۀ RPN یا اولویتبندی ریسک مشخص میشود کدام ابزار کنترل خطا برای شما اثربخش خواهد بود چون هدف PFMEA جلوگیری از بروز عیب است.
همچنین دو محدودیت و ریسک دیگر هم باید بررسی شود: هزینه و زمان
محدودیت اول، بودجهای است که قرار است صرف تجهیز ماشین به ابزارهای پوکا یوکه شود. گاهی دیده شده هزینۀ طراحی، ساخت و نگهداریِ ابزارهای قرنطینه از هزینۀ تولید محصول معیوب و دوبارهکاری آن بیشتر شده است.
محدودیت دوم زمان است. اگر بخواهید جلوی بروز خطا برای محصولی را بگیرید که در حال حاضر هزینۀ زیادی را به سازمان تحمیل میکند و عملاً قطعه با ضرر تولید میشود در گام اول نیاز به ابزارهایِ سادهای دارید که به عنوان یک اقدام فوری به ماشین اضافه شود و جلوی مشکل گرفته شود و سپس یک برنامه تهیه شود تا در طول زمان جلوی بروز عیب به طور کامل گرفته شود.
انواع مختلف خطاها
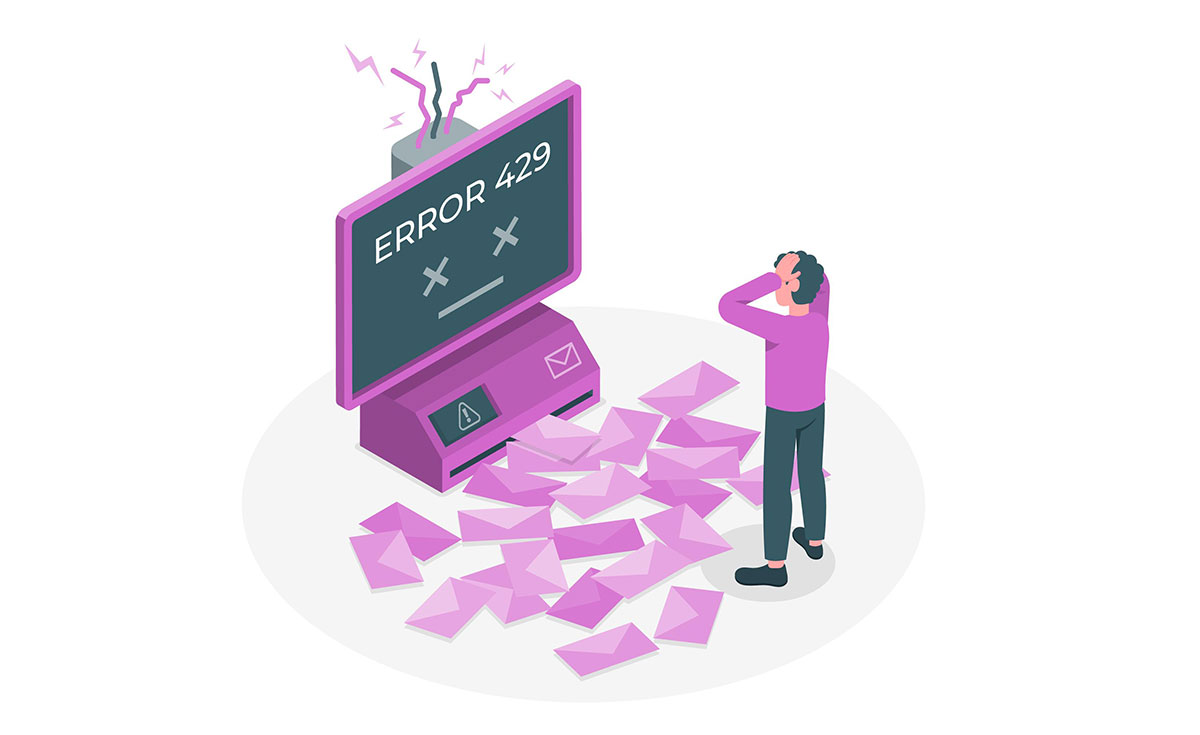
بیشتر عیوب در اثر خطاهای انسانی ایجاد میشوند. خطاهای انسانی نیز به 10 نوع اصلی تقسیم میشوند:
- بیتوجهی یا فراموشکاری: وقتی ما تمرکز نداریم، بعضی چیزها را فراموش میکنیم، مثل وقتی که رئیس ایستگاه فراموش میکند سوزن تعویض خط را جابهجا کند.
راههای پیشگیری: اعلام پیشاپیش به اپراتور و یا بررسی منظم. - خطاهای ناشی از درک اشتباه: گاهی ما مرتکب اشتباه میشویم، چون قبل از آشنا شدن با شرایط محیطی، فورا نتیجهگیری میکنیم. برای نمونه کسی که با خودروی دنده اتوماتیک کار نکرده است پای خود را روی ترمز فشار میدهد، چون فکر میکند کلاچ است.
راههای پیشگیری: آموزش، بررسی قبلی و استاندارد کردن رویه انجام کار. - خطاهای شناسایی: گاهی ما در خصوص یک موقعیت، اشتباه قضاوت میکنیم، چون یا خیلی سریع به آن نگاه میکنیم یا آن موقعیت اینقدر از ما دور است که نمیتوانیم آن را به وضوح تشخیص دهیم. مثلا رنگ دو چراغ قرمز و نارنجی را از دور خوب تشخیص نمیدهیم و به اشتباه دستور به ادامه کار میدهیم.
راههای پیشگیری: آموزش، دقت و احتیاط. - خطاهای ناشی از بیتجربهبودن: گاهی ما به دلیل فقدان تجربه اشتباه میکنیم. مثلا یک کارگر تازهکار نمیتواند کار خود را به خوبی انجام دهد، چون هنوز تجربه لازم را کسب نکرده است.
راههای پیشگیری: ایجاد مهارت در نیروی کار و استاندارد کردن کار. - خطاهای ناشی از خودسری: گاهی ما تحت برخی شرایط قوانین را نادیده میگیریم، برای مثال زمانی که چراغ عابر پیاده، قرمز است از خیابان عبور میکنیم چون در آن لحظه اتومبیل دیگری وجود ندارد.
راههای پیشگیری: آموزش اولیه و افزایش تجربه. - خطاهای غیرعمد: گاهی ما به دلیل حواسپرتی و بیآنکه متوجه شویم، اشتباه میکنیم. برای مثال برای فردی که غرق در افکار خودش است، بدون توجه به اینکه چراغ عابر قرمز است، سعی میکند از خیابان عبور کند.
راههای پیشگیری: دقت منظم و استاندارد کردن کار. - خطاهای ناشی از کندی: گاهی ما به دلیل تاخیر در انجام قضاوت، کارها را به کندی انجام میدهیم و درنتیجه دچار اشتباه میشویم. به عنوان مثال شخصی که در حال یاد گرفتن رانندگی است، پای خود را دیر روی ترمز میگذارد.
راههای پیشگیری: پیشگیری، کسب مهارت و استاندارد کردن کارها. - خطاهای ناشی از فقدان استاندارد: بعضی از خطاها به دلیل فقدان دستورالعملهای مناسب و استانداردهای کاری اتفاق میافتد. مثل اندازهگیریهایی که منوط به قضاوت کارگران میشوند.
راههای پیشگیری: استاندارد کردن کار و تدوین دستورالعمل و استانداردهای کاری. - خطاهای غیرمنتظره: گاهی خطاها زمانی رخ میدهند که تجهیزات مطابق انتظار کار نمیکنند. برای مثال وقتی یک ماشین بدون اعلام قبلی بد عمل میکند.
راههای پیشگیری: تعمیرات بهرهور فراگیر (TPM) و استاندارد کردن کار. - خطاهای عمدی: بعضی از افراد عمدا اشتباه میکنند. خرابکاریها از این نوع خطاها به حساب میآیند.
راههای پیشگیری: آموزش اولیه و نظم.
با اینکه اشتباهات به دلایل مختلفی اتفاق میافتند ولی اغلب آنها قابل پیشگیری هستند، به شرط آنکه زمانی را صرف کنیم تا بفهمیم این اشتباهات کجا و کی اتفاق میافتند و در جهت جلوگیری از بروز آنها با استفاده از روشهای پوکا یوکه و پیشگیریهای گفتهشده در این بخش، اقدام کنیم.
پوکا یوکه برای چه کسب و کارهایی مفید است؟
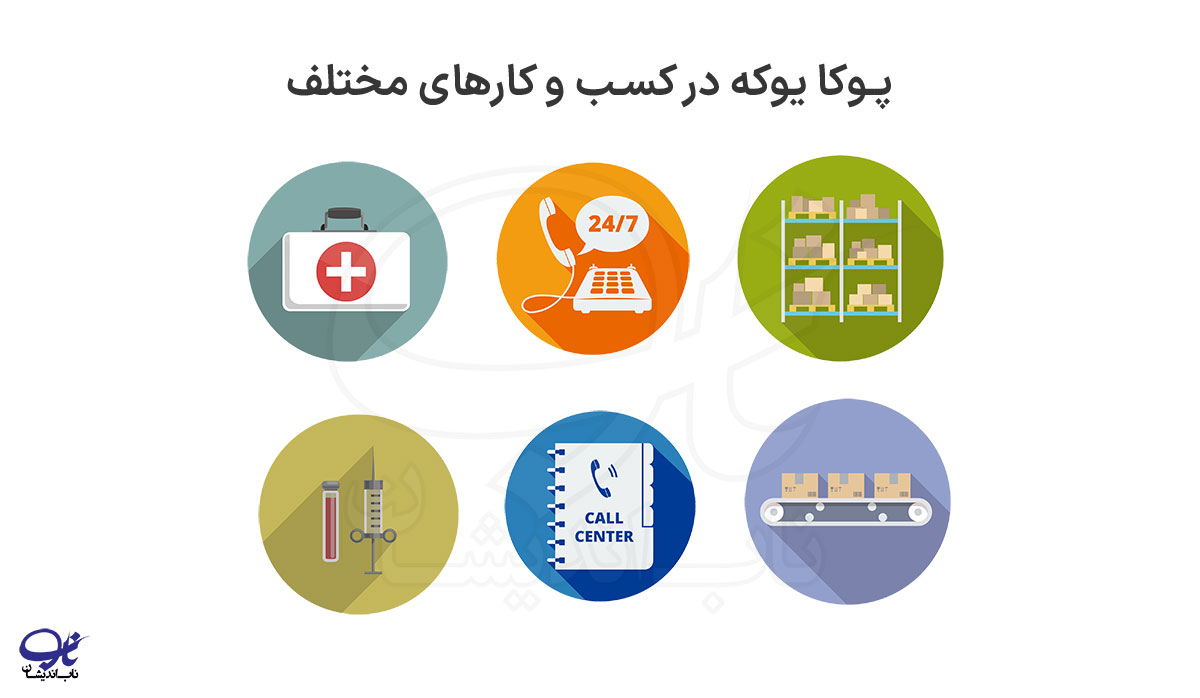
پوکا یوکه را میتوان در موقعیتها و صنایع مختلفی به کار برد که در آن کیفیت و جلوگیری از خطا حیاتی است. در اینجا برخی از فرایندهای رایج که پوکا یوکه در آنها قابل پیادهسازی است را با هم مرور میکنیم.
۱. فرایندهای تولید و مونتاژ:
پوکا یوکه به طور گسترده در فرایندهای تولید و مونتاژ برای جلوگیری از خطا و نقص استفاده میشود. هدف اطمینان از مونتاژ صحیح قطعات، تراز مناسب قطعات و اجرای دقیق فرایندها است. به این شکل بسیاری از دوبارهکاریها و ضایعات کم شده و در کل کارایی و کیفیت افزایش پیدا میکند.
۲. ارائه خدمات:
پوکا یوکه را همچنین میتوان در فرایندهایی برپایه خدمات اعمال کرد. به عنوان مثال، در خدمات مشتری، تکنیکهای پوکا یوکه میتواند به جلوگیری از خطا در پردازش سفارش، صدور صورتحسابها یا ورود اطلاعات کمک کند. با پیادهسازی مکانیسمهای ضد خطا، رضایت مشتری افزایش پیدا میکند، اشتباهات به حداقل میرسند و بهبود کلی در ارائه خدمات انجام میشود.
۳. مراقبتهای بهداشتی و ایمنی بیمار:
در مراکز درمانی، از تکنیکهای پوکا یوکه میتوان برای ایمنی بیمار و جلوگیری از خطاهای پزشکی استفاده کرد. به عنوان مثال، استفاده از سیستم های اسکن بارکد برای اطمینان از اینکه داروی مناسب به بیمار مناسب داده میشود، یا اجرای چکلیستها و پروتکلها برای کاهش خطر خطاهای جراحی.
۴. مدیریت انبارها و موجودی:
تکنیکهای پوکا یوکه در مدیریت موجودیها و متعاقبا تکمیل سفارشات، بسیار با ارزش خواهد بود. به عنوان مثال، استفاده از سیستمهای کنترل موجودی خودکار برای دانستن موجودی دقیق محصولات در انبارهای مختلف. این تکنیکها میتوانند دقت در تعیین تعداد موجودیهای در دسترس را افزایش داده، کمبود کالا را کاهش دهند که خود به خود باعث افزایش رضایت مشتری میشود. اثرگذاری این ابزارها وقتی به حداکثر میرسد که با سیستم کانبان و کنترل دیداری همراه باشند.
در مجموع، پوکا یوکه را میتوان در هر موقعیتی که خطا یا نقصی رخ میدهد، صرفنظر از صنعت یا یک فرایند خاص، به کار برد. هدف اصلی آن جلوگیری از اشتباهات، ارتقاء کیفیت و بهبود کلی بهرهوری عملیاتی است.
8 اصل موثر برای شناسایی و پیشگیری از خطاها
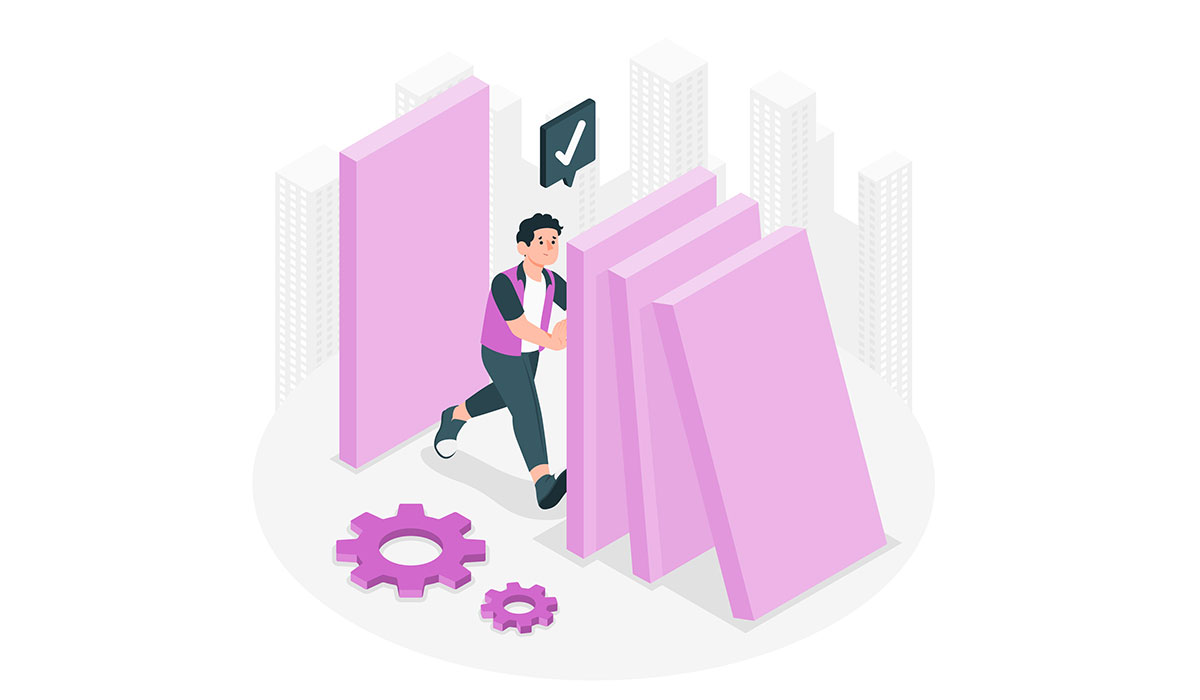
- کیفیت را با فرایندها ادغام کنید.
این کار، وقتی خطایی اتفاق میافتد، تولید محصول معیوب را غیرممکن میکند. تکنیکهای رسیدن به این هدف، بازرسی صددرصدی با استفادۀ از ابزارهای پیشگیرانه مانند هشداردهندهها است مثل استفاده از جیگهایی که بخشی از فرایند تولید اند. - تمام خطاها و عیوب مضر را میتوان حذف کرد.
ما باید فرض کنیم اشتباهات اجتنابناپذیر نیستند. جایی که یک اراده قوی وجود داشته باشد راهی برای حذف تمام خطاها و اشتباهات پیدا خواهد شد. - انجام کار اشتباه را متوقف و انجام کار صحیح را از هم اکنون آغاز کنید.
بیایید به طور کلی “اماها” را از جملاتمان حذف کنیم، جملاتی مثل «میدانیم که این کار درست نیست اما مجبوریم فعلا انجامش دهیم» و … به جای این حرفها بلافاصله جلوی انجام کار اشتباه را بگیرید. - به بهانه فکر نکنید به «چگونه درست انجام دادن» فکر کنید.
به جای اینکه به بهانه فکر کنیم، بیاییم به این فکر کنیم که چگونه میتوان کارها را به درستی انجام داد. - برای موفقیت، یک شانس 60 درصدی به اندازه کافی خوب است، پس همین الان ایدهتان را اجرا کنید.
برای دستیابی به بهبود لازم نیست قبل از دست زدن به عمل به هدف کمال رسید. شما باید علت را تجزیه و تحلیل کنید و بعد به پیدا کردن راهحل فکر کنید. اگر شانس موفقیت راهحل شما بیش از 50% باشد، آن را به اجرا درآورید. شما میتوانید راهحل خود را با توجه به نتایج به دست آمده، بعدا اصلاح کنید. - وقتی همه با هم در جهت حذف اشتباهات و عیوب همکاری کنند، عیوب به صفر کاهش پیدا میکنند.
با یک آدم تنها نمیتوان به اشتباهات و عیوب صفر رسید، این بسیار مهم است که همه در سرتاسر سازمان با همکاری همدیگر اشتباهات و عیوب را حذف کنند. - چند فکر بهتر از یکی است.
طوفان ذهنی هر کسی دارای اهمیت است، اما عقل و خلاقیتی که ناشی از کوششهای چند نفر باشد خیلی باارزشتر است. کار تیمی کلید رسیدن به ایدههای موثر برای بهبود است. - با استفاده از «5 چرا» و «یک چطور» به جستجوی علت واقعی باشید.
وقتی محصولی معیوب میشود، شما نباید تعداد بازرسها را بیشتر کنید و به جای این کار باید به ریشه مشکل پی ببرید تا اطمینان پیدا کنید که راه حل شما واقعی است و نه یک ایده سرهمبندی شده! شما باید بپرسید: «چرا این محصول معیوب شده است؟» و در برابر جوابی که داده میشود دوباره بپرسید «چرا؟». به علتهایی که به آسانی به ذهن میرسند، راضی نشوید و باز هم بپرسید «چرا؟» حداقل 5 بار بپرسید چرا تا ریشه مشکل را کشف کنید. پس از آن باید بپرسید: «حالا چطور میتوانیم مشکل را حل کنیم؟» و آن موقع باید راهحل واقعی را اجرا کنید.
وضعیت به کارگیری پوکا یوکه در ایران
(1) اگر نگوییم همه، اکثر شرکتهای ایرانی واحدی به نام کنترل کیفیت (Quality Control/QC) دارند. کارشناسهای این واحد با دقت و وسواس، محصول را در طول عملیات تولید –مانند تولید یک قطعه- بازرسی میکنند یا در نقاط مختلف یک فرایند اداری/خدماتی حضور دارند –مثلا در بانک، صندوقهای بازنشستگی و …- تا عیوب را شناسایی کنند و بازخورد دهند. اما باز هم شاهد خروج محصول معیوب از انبار یا ارائه خدمات ناقص به مشتریها هستیم مانند خودروساز که قطعهسازها را برای حتی یک قطعۀ معیوب جریمه و کل سفارش را بازمیگردند یا فروشگاههای زنجیرهای که به دلیل محصول معیوب شرکت تولیدکننده را جریمههای هنگفت میکنند یا حتی وقتی نرمافزار مورد تقاضای مشتری آنطور که میبایست عمل نمیکند و باگ دارد و …. .
در این شرکتها واحد کنترل کیفیت باید یک گام به جلو بر دارد و از QC به ZQC مبدل شود. اضافه کردن Zero حاکی از آن است که بازرسیِ حینِ فرایند و تشخیص محصول معیوب خوب است اما کافی نیست. باید کاری کنیم که جلوی محصول معیوب یا خدمت ناقص گرفته شود پیش از آنکه تولید یا ارائه شوند و حتی اگر کارکنان بخواهند اشتباه کنند. رسیدن به هدفِ تولید محصولاتی با خرابی/عیوبِ صفر یا ارائۀ خدماتی با نقص/اشتباه صفر یک کارِ فرا واحدی است که تحت نظارت و مدیریت واحد کنترل کیفیت انجام میشود.
(2) وقتی هم شرکتها به این آگاهی میرسند معمولا تمایل دارند از کُچهای (Coach) بیرونی برای استقرار سیستمهای کنترل کیفیت صفر استفاده کنند. اما کُچ فقط میتواند دانش و تجربۀ خود را در اختیار سازمان قرار دهد و هیچ نسخۀ از پیش نوشته شدهای وجود ندارد. معمولا بسیاری از ابزارهای خطاناپذیرسازی توسط تیمهایی طراحی و پیادهسازی میشوند که متشکلاند از مدیران یا کارشناسهایِ واحدهای کنترل کیفیت، نگهداری و تعمیرات، تولید و حتی اپراتوری که کار را انجام میدهد و گاهی هم بسته به نیاز واحد تکوین و توسعه هم به این تیم اضافه میشود. فقط در این صورت است که میشود ضمانت داد تکنیک پیاده شده تثبیت و حفظ خواهد شد.
(3) مشکل مهم دیگری که در ایران با آن مواجهایم، این تفکر غلط است که میتوان از ابزارهای پوکا یوکه به تنهایی و بدون پیادهسازی کل سیستم تولید ناب استفاده کرد. اما همانطور که در قبل هم گفته شده است ابزارهای پوکا یوکه وقتی درست عمل میکنند و به اثربخشی صددرصدی میرسند که در کنار ابزارهایی مثل حلمسئله، سیستم نت، سیستم کانبان، کار استاندارد، ساماندهای محیط کار و ایجاد یک محیط کاری خود گویا یا دیداری و ممیزیهای لایهایِ روتین انجام شوند. بدون این ابزارها یا تکنیکها، تکنیکهای پوکا یوکه خیلی زود از کار میافتند یا به درستی از آنها استفاده نمیشود.
سخن پایانی
اما مسئولیت موفقیت در رسیدن به عیوب صفر، نهایتا برعهده مدیریت است. رهبران یک سازمان باید تصوری از کیفیتی داشته باشند که شرکت قادر به ایجاد آن است و همچنین باید فرهنگ و محیطی در سازمان به وجود آورند که کارکنان را علاقمند کند که آنها هم به چنین باوری برسند. منظور این است که باید برای گروههای کاری، زمان و منابع لازم برای تحلیل مشکل در نظر گرفته شود. معمولا سیستمهای نظام- پیشنهادات اگر درست کار شوند کارکنان تشویق میشوند مشکلات را شناسایی و حل کنند تا محصول معیوب تولید نشود یا خدمت ناقصی ارائه نشود. برای رسیدن به این هدف، باید تواناییهای فنی افرادی که کارها را انجام میدهند، شناسایی شده و مکانیزمی ایجاد شود که بتوانند دانش خود را با دیگران به اشتراک بگذارند. سرانجام مهمتر از همه اینکه باید محیطی ایجاد شود که کارکنان بخواهند دانش خود را در جهت منافع شرکت با همکارانشان به اشتراک بگذارند.
یادمان باشد پوکا یوکه یکی از ابزارهای تولید ناب است و بدون پیادهسازی کل این سیستم و استفاده صرف از ابزارهای پوکا یوکه در عمل نتایج کمی در بر خواهد داشت. خود سیستم تولید ناب و تکنیکهای آن از جمله سیستم حرکت پیوسته، کار استاندارد، کانبان و …. به خودی خود نوعی پوکا یوکه هستند و از بروز بسیاری از عیوب جلوگیری میکنند در عین این که زیرساختهایی فراهم میآوردند که امکان استفاده درست از ابزارهای پوکا یوکه را میسر میکنند.